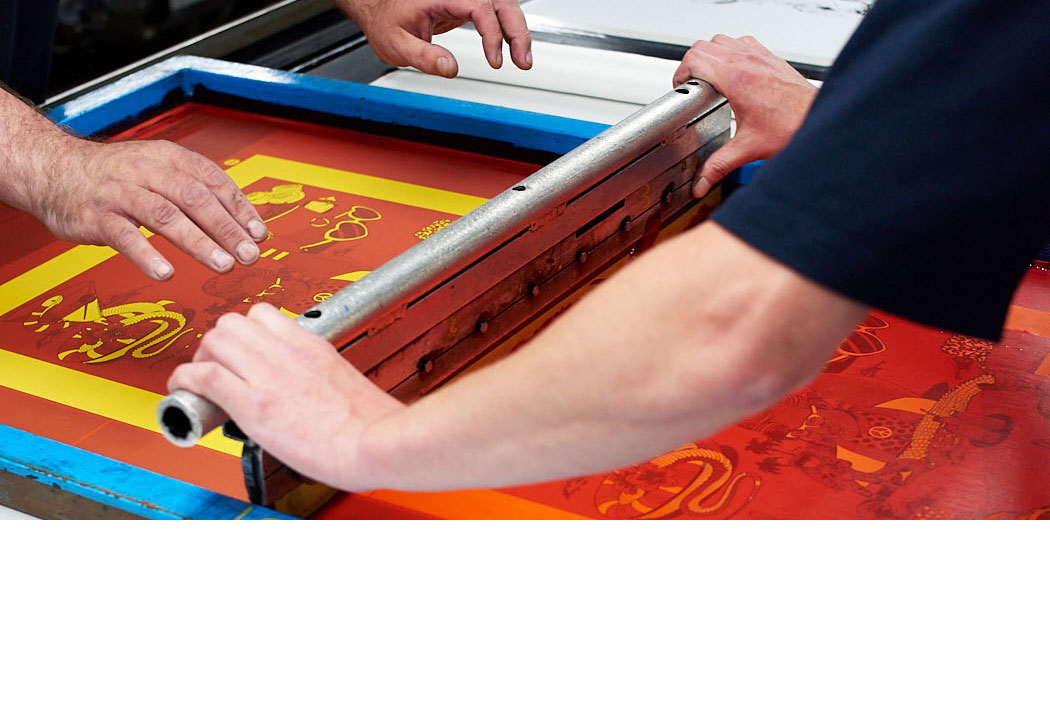
Everything You Need to Know About Screen Printing - MVA Design & Supply
November 13, 2024
Introduction:
Welcome to the vibrant world of screen printing! Whether you're looking to create custom screen-printed tee shirts, interested in the mechanics of a garment screen printing machine, or curious about the materials for screen printing on fabric, you've come to the right place. MVA Design & Supply is your ultimate guide, providing insights, tips, and tricks to master the screen print function. From screening shirts to exploring the vast universe of screen printing materials, we'll dive deep into every aspect of this versatile printing technique.
.png)
Screen Printing Explained: The Art of Imprinting Designs
At its core, screen printing is a technique that involves transferring a stenciled design onto a flat surface using ink, a mesh screen, and a squeegee. Though traditionally linked with fabric, this versatile method extends its reach to metal, plastic, glass, wood, and more, making it a favorite across various industries. Known also as silk-screen printing or serigraphy, screen printing has carved its niche for its vibrant colors and ability to tackle dark fabrics with ease.
The Screen Print Function: How Magic Happens
The process of screen printing is akin to painting with a stencil, yet it unfolds on a more complex and precise scale. This intricate dance begins when a design is printed onto a transparent acetate film, which then acts as a guide for creating the stencil. The real enchantment happens when this design is transferred onto a mesh screen that's been coated with a light-reactive emulsion. Under bright light, the emulsion surrounding the design hardens, while the areas of the design itself remain untouched and soft. These soft areas are then washed away, revealing a stencil that's ready for ink application.
The application of ink over this stencil is where the technique truly shines. The ink is pressed through the mesh screen with a squeegee, transferring the design onto the printing surface below. This method allows for the creation of sharp, vivid designs that boast an impressive level of detail and color fidelity. The ability to layer inks through multiple stencil applications also opens the door to multi-colored designs, adding depth and life to the final product. The outcome? A striking, vibrant design that captures the essence of the original concept with fidelity and flair.
Materials for Screen Printing on Fabric: Choosing the Right Tools
In the realm of screen printing, the choice of materials can significantly influence the quality and appearance of the final product. Ink selection is paramount, with two primary options dominating the scene: plastisol and water-based inks. Plastisol inks are celebrated for their durability and vibrancy, making them a favorite for projects that demand bold, lasting colors. On the other hand, water-based inks are lauded for their softer texture and environmental friendliness, offering a gentler alternative that's easier on fabrics and the planet alike.
The choice of fabric also plays a critical role in the screen printing process. Cotton and cotton blends are often preferred for their ability to absorb ink effectively, providing a smooth, even canvas for the design. However, the screen's mesh count — the number of threads per inch — also influences the final outcome. Higher mesh counts allow for finer detail and thinner ink deposits, ideal for intricate designs and delicate fabrics. Conversely, lower mesh counts are better suited for bold, graphic designs and thicker ink layers, offering versatility to accommodate a wide range of artistic visions.
The Heart of Screen Printing: Machines That Bring Designs to Life
At the heart of the screen printing process lie the machines that bring designs from concept to reality. Screen printing machines, whether they are garment screen printing machines or screening printing machines, are engineered to accommodate projects of all sizes, from simple one-color prints to complex multi-color designs. The market is flush with options, ranging from manual presses ideal for artisanal, small-scale projects to automated systems designed for efficiency and high-volume production.
When selecting a screen printing machine, several features warrant consideration. The number of stations on the press determines how many colors can be printed simultaneously, a crucial factor for multi-colored designs. The machine's adjustability, including its ability to accommodate screens of different sizes and adjust to various substrates, is also vital for versatility. Furthermore, compatibility with the chosen printing materials — from inks to substrates — ensures a seamless, efficient printing process. Each machine offers a unique set of capabilities, allowing printers to select the perfect tool for their specific needs and creative ambitions.
Custom Screen Printed Tee Shirts and Beyond: A Canvas for Creativity
Screen printing's versatility shines brightest in the world of custom apparel, particularly with custom screen-printed tee shirts. This method offers unparalleled quality and durability, ensuring that designs withstand the rigors of wear and washing. The crisp, vibrant results of screen printing make it the method of choice for producing high-quality, enduring designs on a variety of apparel items.
However, the potential applications of screen printing extend far beyond clothing. From promotional items like bags and posters to artistic endeavors on canvas and wood, screen printing offers a boundless canvas for creative expression. Its ability to adapt to different materials and surfaces makes it a versatile tool for artists, designers, and businesses alike, enabling the creation of unique, custom items that capture the imagination and stand the test of time. Whether you're creating a line of bespoke apparel or crafting one-of-a-kind artworks, screen printing offers the tools and flexibility to bring your creative vision to life.
Tips and Tricks for Screen Printing Mastery
Achieving mastery in screen printing requires patience, practice, and a bit of insider knowledge. Here are some quick tips:
- Prep is Key: Properly preparing your screen and materials can make or break your project.
- Test Runs: Always do a test print on a similar material to ensure the design and colors come out as expected.
- Cure Correctly: Ensure your ink is properly cured to avoid fading or washing out.
- Cleanliness Counts: Keep your screens and work area clean to prevent accidental smudging or ink contamination